Bloom maximizes the usage of plant material with cutting-edge science.
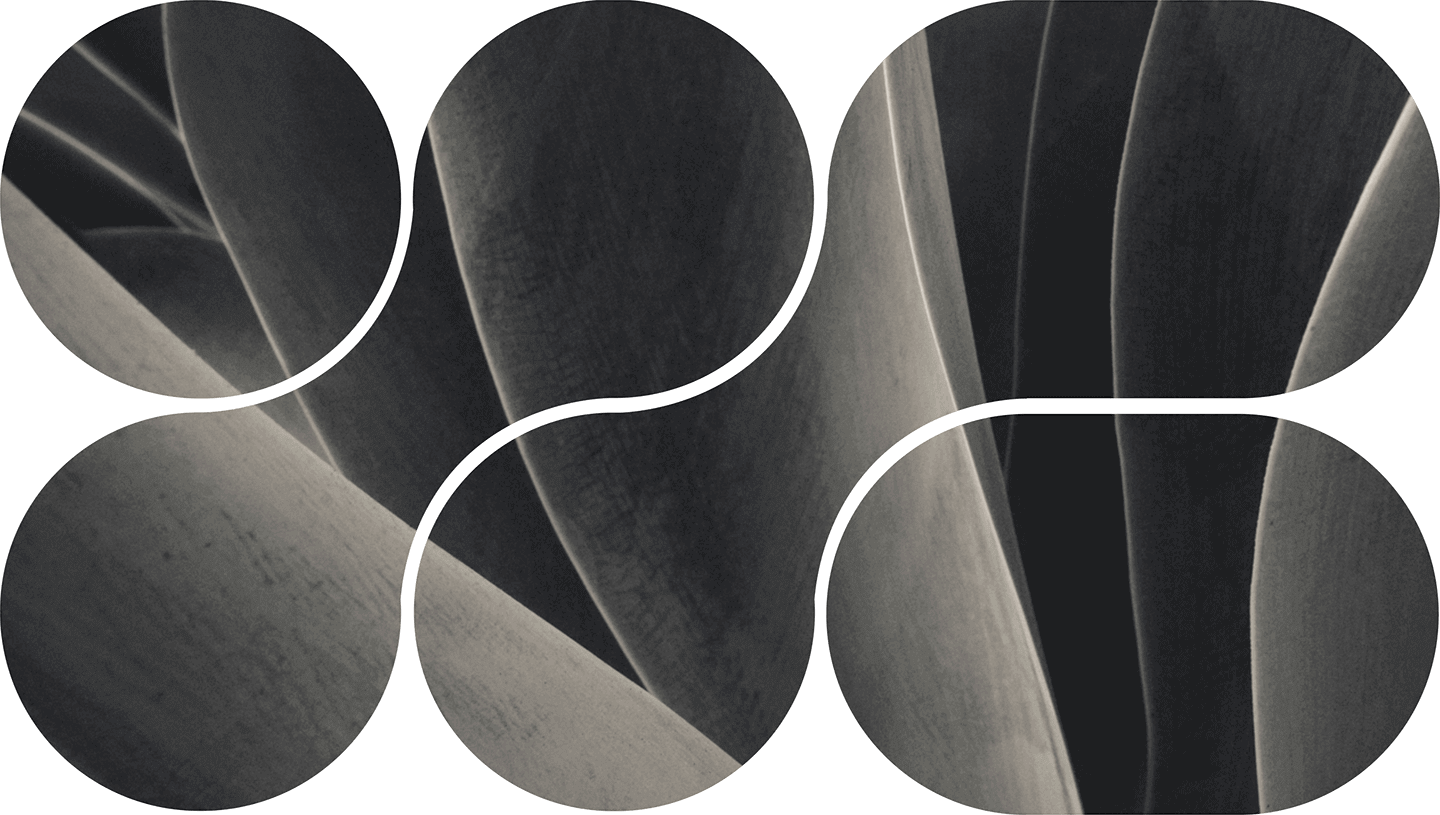
Bloom maximizes the usage of plant material with cutting-edge science.
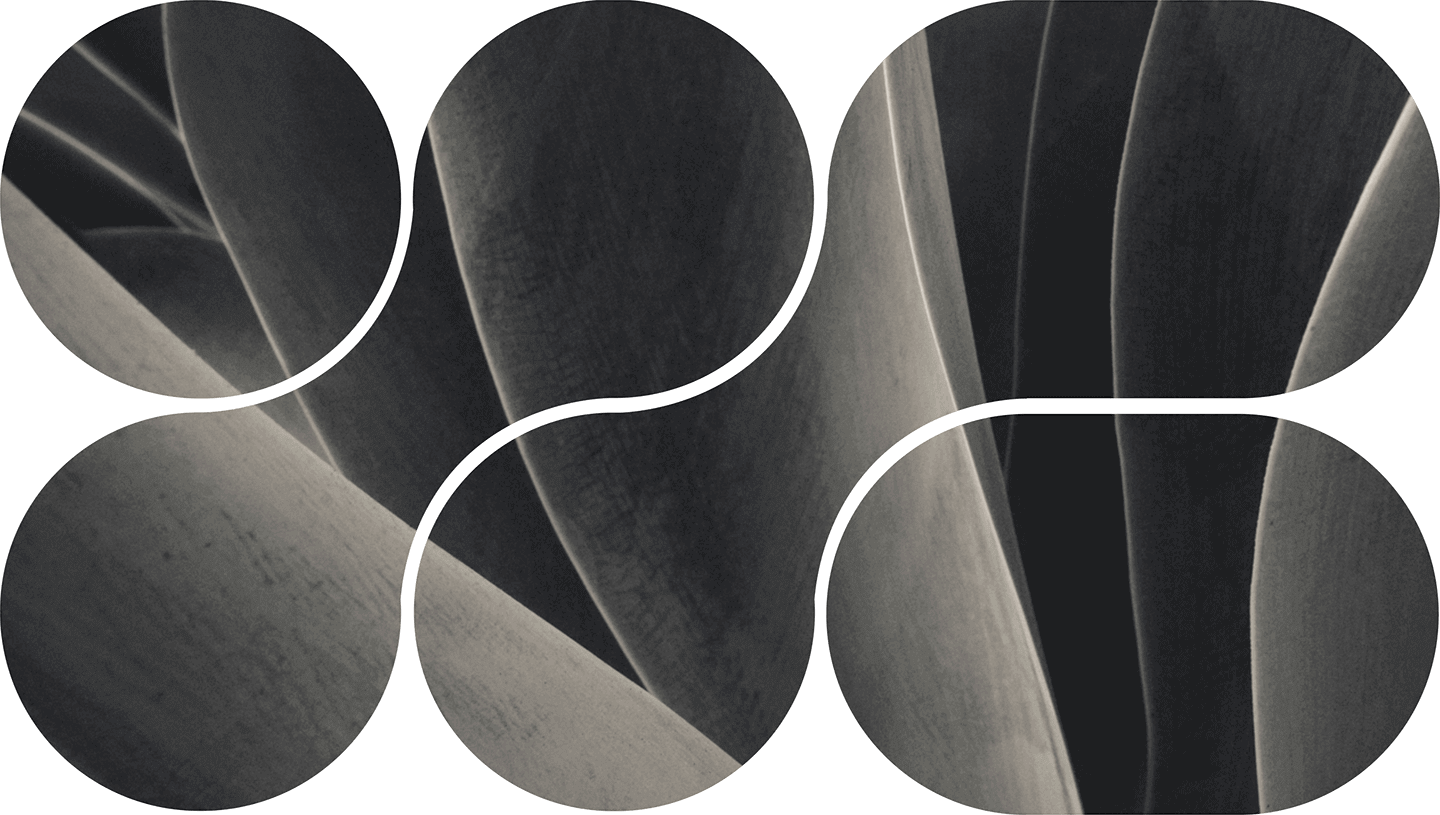
Our technology offers the possibility to break through current limitations. With our aldehyde-assisted fractionation (AAF) technology, we efficiently separate the cellulose fraction while stabilizing lignin polymers and hemicellulose-derived sugars. These stabilized structures allow, for the first time, the full potential of lignin and hemicellulose to be valorized.
Our Plant.
Breaking it down.
How our technology works.
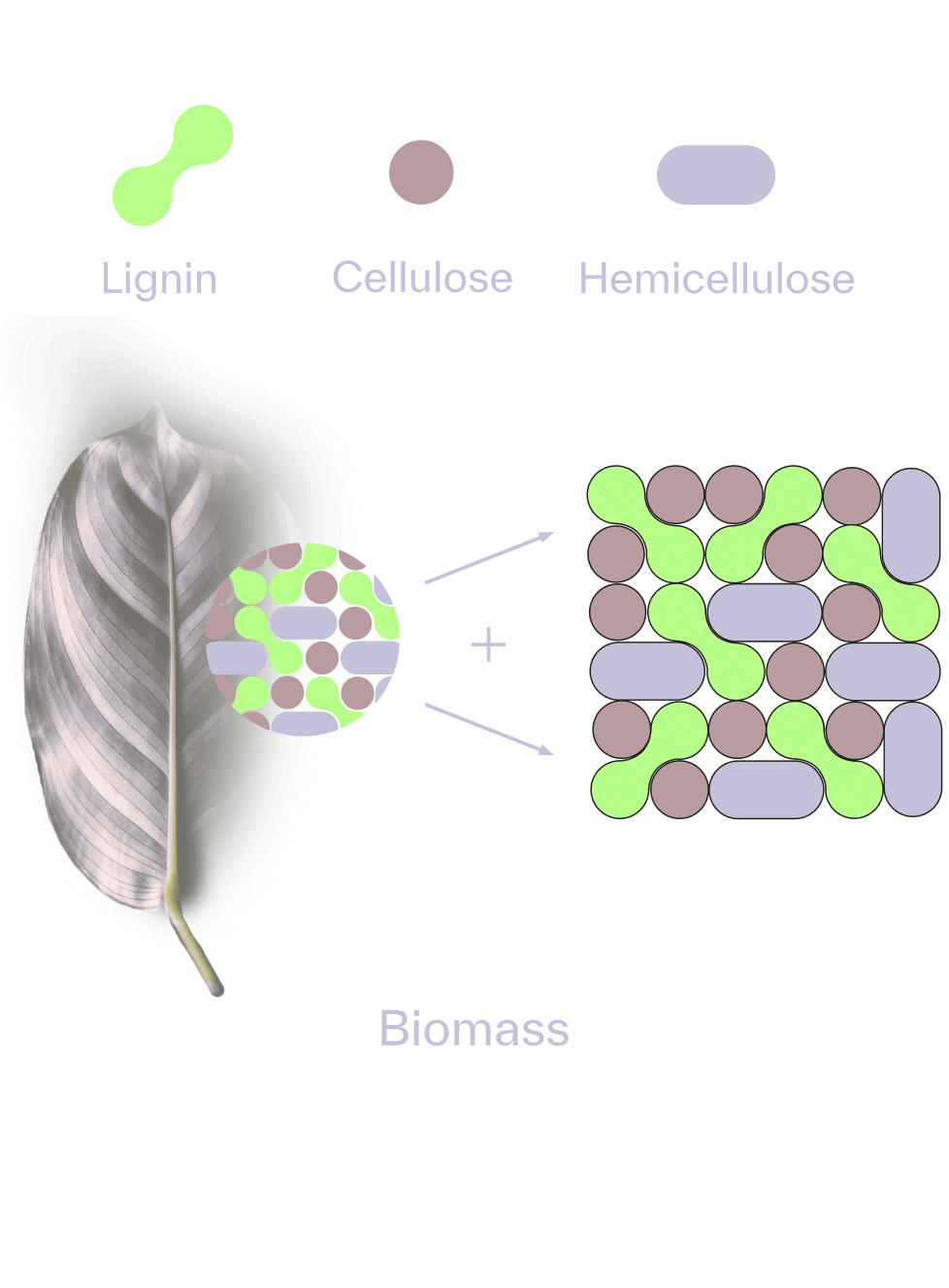
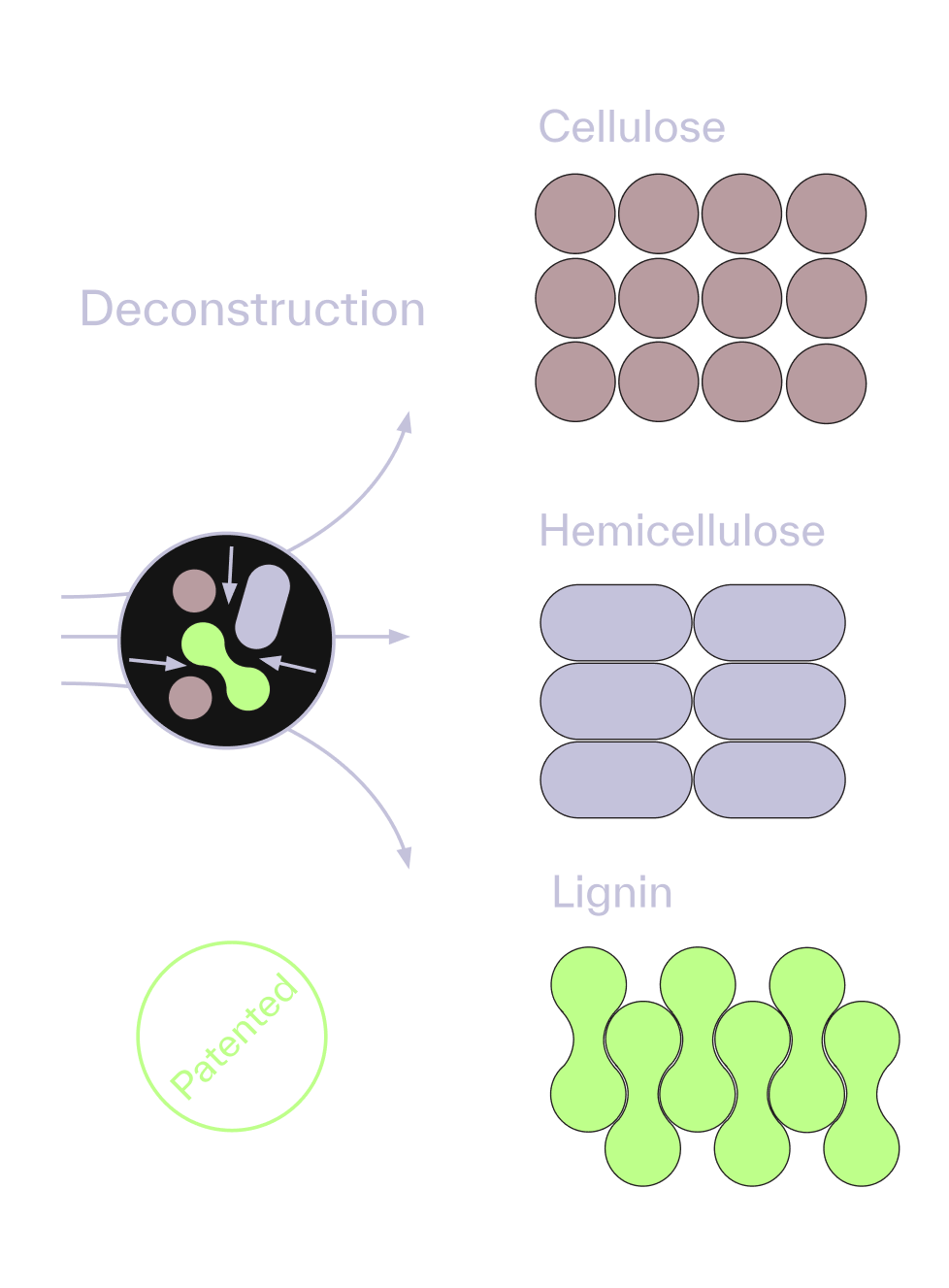
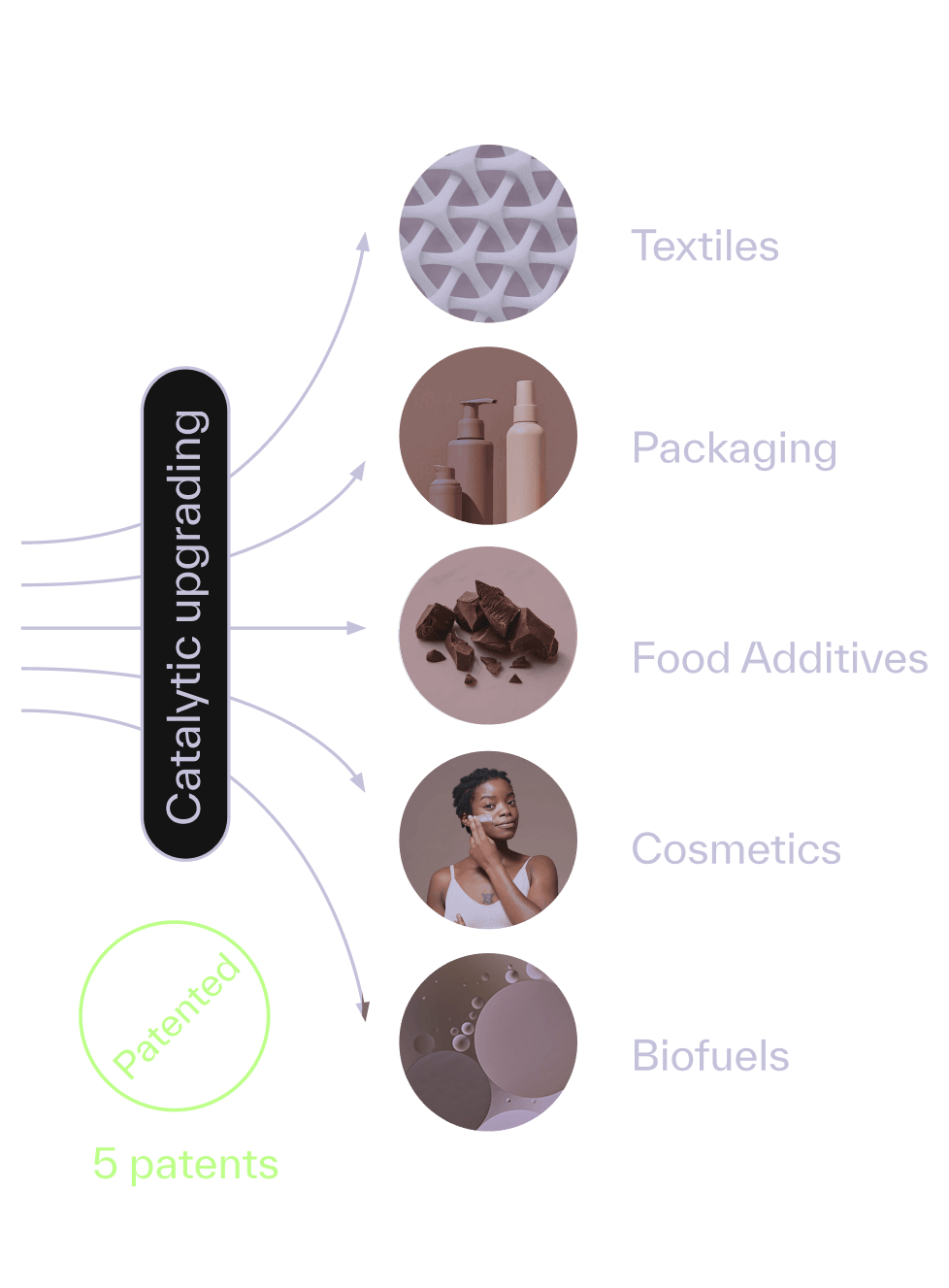
Projects.
In addition to projects developed with our customers, Bloom is grateful to support from public funding.
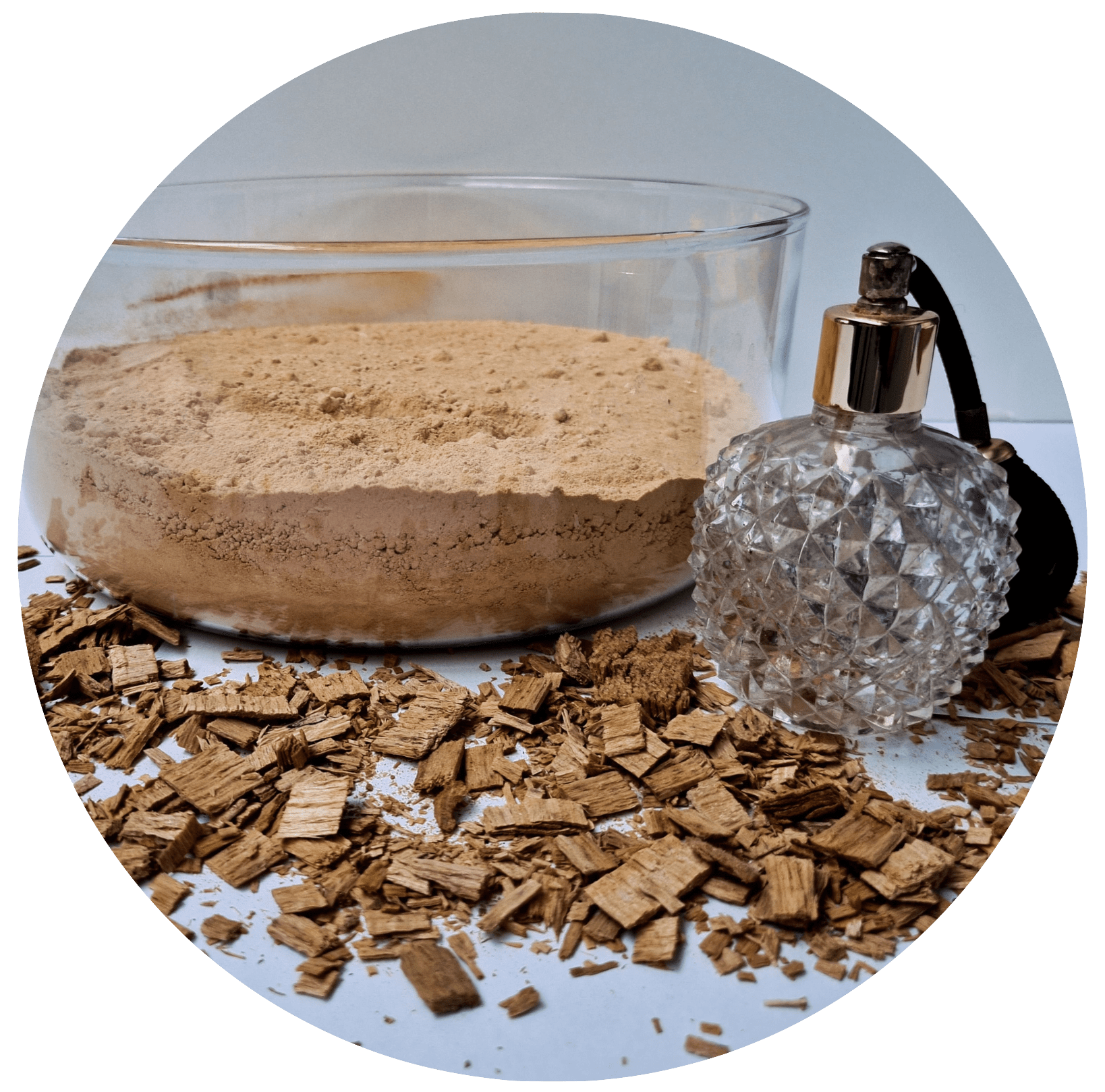
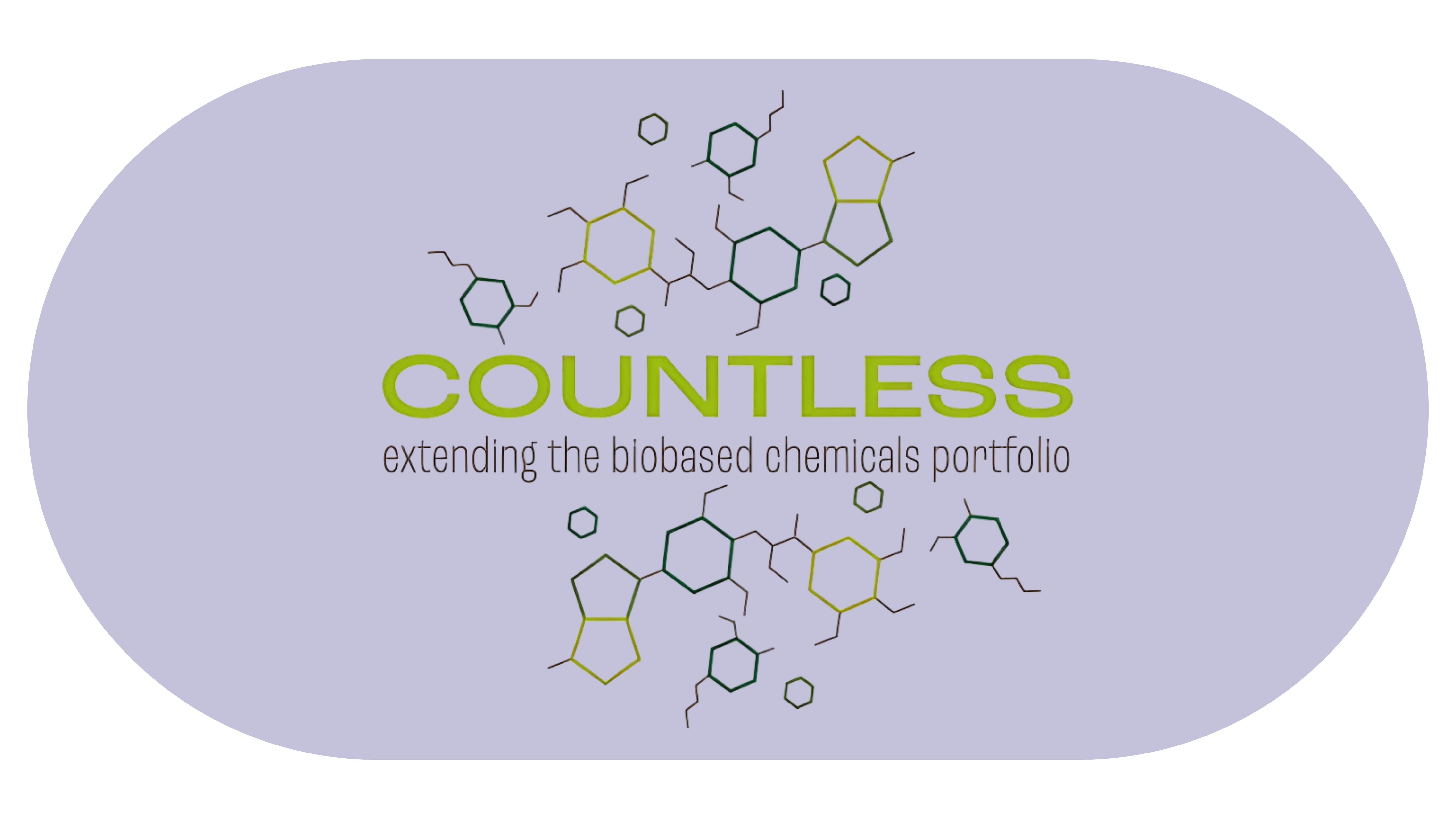
Development of a lignin-based value chain towards market implementation.
This work has received funding from the Swiss State Secretariat for Education, Research and Innovation (SERI). This project has received funding from the Circular Bio-Economy Joint Undertaking under the European Union’s Horizon 2020 research and innovation programme under grant agreement No 792061.
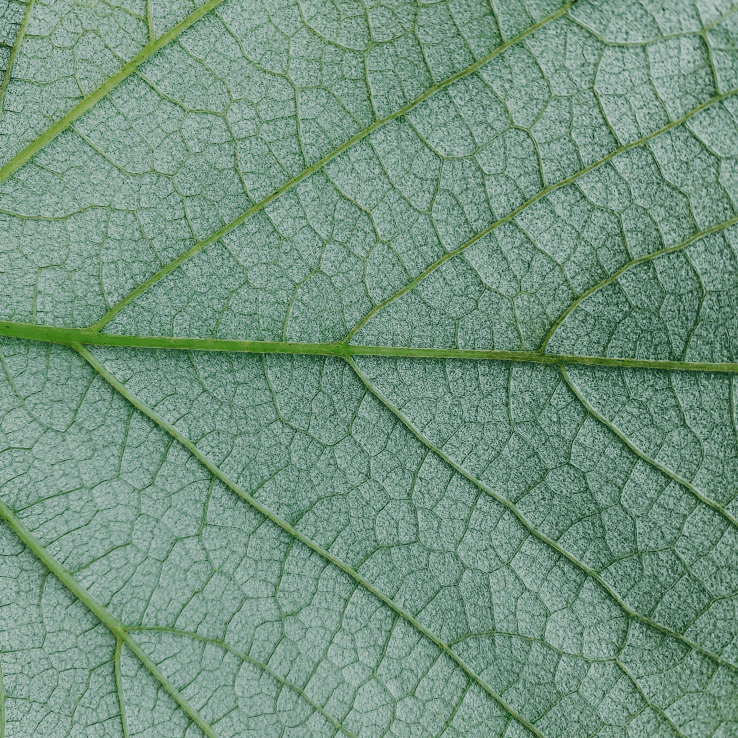
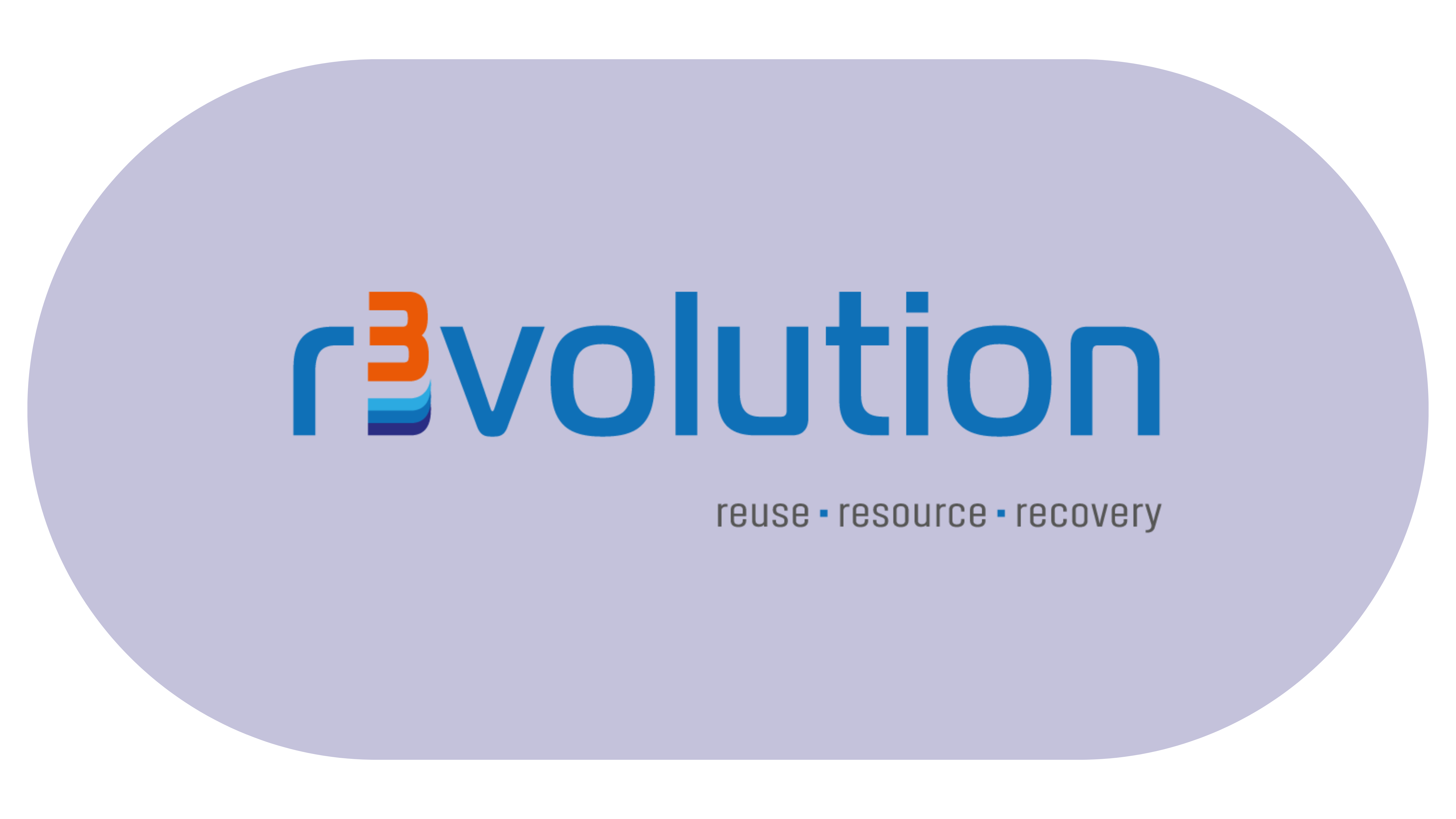
Topic: HORIZON-CL4-2023-TWIN-TRANSITION-01-40 — Sustainable and efficient industrial water consumption: through energy and solute recovery
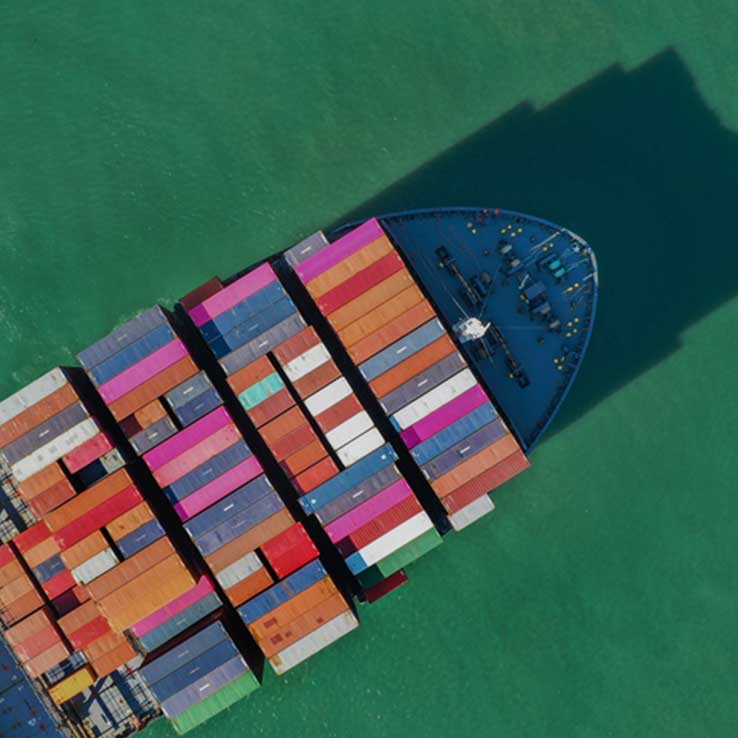
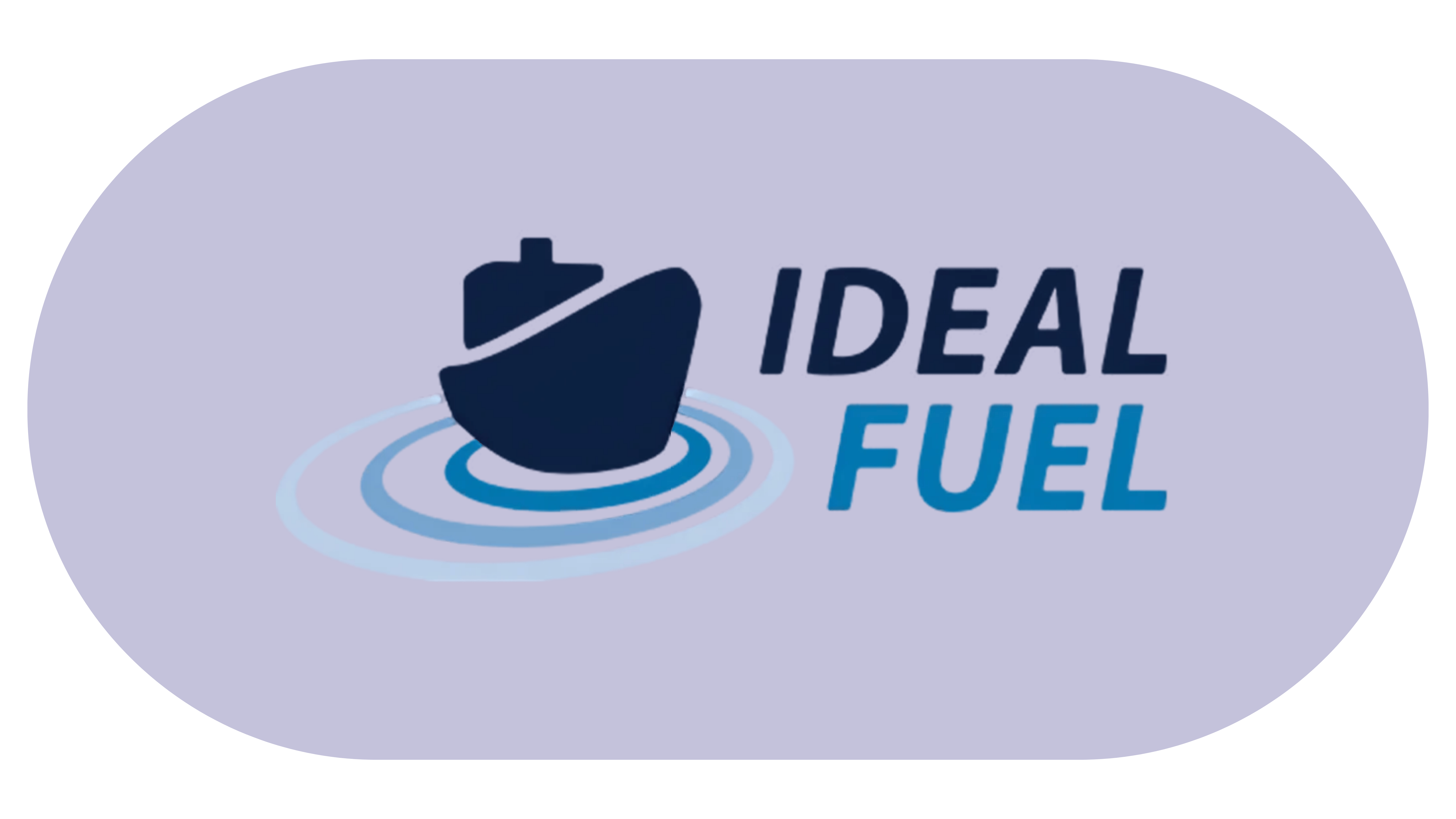
Aims to develop ‘Biogenic Heavy Fuel Oil’ (Bio-HFO) with ultra low sulfur levels that can be used as a shipping fuel within the maritime industry.
This project has received funding from the European Union’s Horizon 2020 research and innovation programme under GA Number 883753.
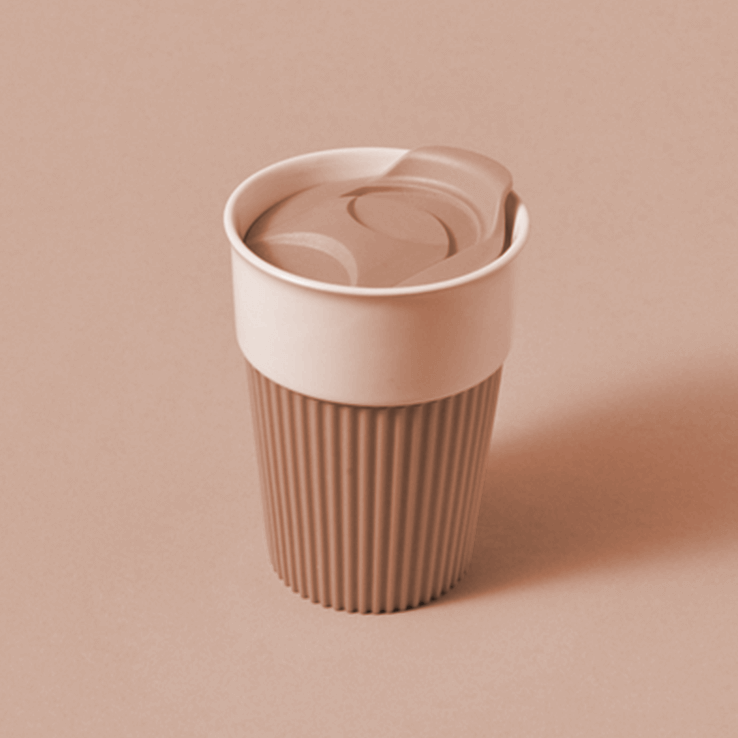
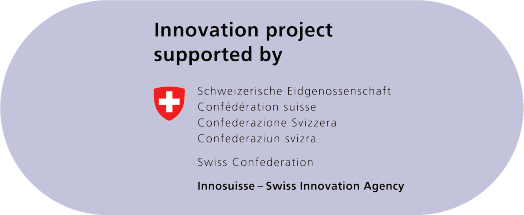
Lignin and its derivatives as additives, fillers, and reagents for bio-based high-performance materials and composites for the plastics industry
Project supported by Innosuisse under project number 105.737 IP-ENG in collaboration with HEIA-FR - Haute école d'ingénierie et d'architecture.
Seal of excellence.
- Shuai et al., Science 2016, 354, 6310, p. 329-333. Formaldehyde stabilization facilitates lignin monomer production during biomass depolymerization.
- Lan et al., Angew. Chem. 2018, vol. 57, num. 5, p. 1356-1360. Protection Group Effects During α,γ-Diol Lignin Stabilization Promote High-Selectivity Monomer Production.
- Questell-Santiago et al., Nature Chemistry 2018, 10, 12, 1222-1228. Carbohydrate stabilization extends the kinetic limits of chemical polysaccharide depolymerization.
- Amiri et al., Nature Protocols 2019, 14, 921-954. Fractionation of lignocellulosic biomass to produce uncondensed aldehyde-stabilized lignin.
- Héroguel et al., ACS Sustainable Chem. Eng. 2019, 7, 20, 16952-16958. Catalyst support and solvent effects during lignin depolymerization and hydrodeoxygenation.
- W. Lan et al., Green Chemistry 2021, 23, 1, 320-327. Continuous hydrogenolysis of acetal-stabilized lignin in flow.
- J. B. de Bueren et al., ACS Sustainable Chemistry & Engineering 2020, 8, 45, 16737-16745. Aldehyde-Assisted Fractionation Enhances Lignin Valorization in Endocarp Waste Biomass.
- R. Vendamme et al., Biomacromolecules 2020, 21, 10, 4135-4148. Aldehyde-Assisted Lignocellulose Fractionation Provides Unique Lignin Oligomers for the Design of Tunable Polyurethane Bioresins.
- Y. M. Questell-Santiago, ACS Sustainable Chemistry & Engineering 2020, 8, 4, 1709-1714. Catalyst Evolution Enhances Production of Xylitol from Acetal-Stabilized Xylose.
- L. P. Manker et al., Nature Chemistry 2022, Sustainable polyesters via direct functionalization of lignocellulosic sugars.
- S. Bertella et al., ChemSusChem 2022, Extraction and Surfactant Properties of Glyoxylic Acid‐Functionalized Lignin.
FAQ.
Bloom focuses on sustainably harvested biomass where there is no competition with food production. We have demonstrated the potential of our technologies with under-utilized resources such as sawmill residues, and agricultural side streams such as straw or wastes from the food industry; e.g. hazelnuts shells. The availability of these feedstocks is estimated to be 10 billion tons/year which is an order of magnitude higher that the consumption of petrochemicals (730 million tons/year) for materials.
We focus on our core expertise, breaking down biomass to its core elements, and we rely on partners with existing production capacity to cover the end of the value chain. They just need to switch their sourcing from current petro-based solutions to Bloom’s sustainable ingredients. Hence, we typically do not sell the end-product ourselves.
Bloom leverages the learnings from hundreds of years of petro-industry operations and combines it with state of the art biomass valorisation principles to match the low prices and high performances of petro-based products, which are the current market benchmark.
It all depends on the boundaries of the life cycle assessment (LCA). If you only consider the material production (eg. Cradle to gate), the CO2 storage from plants can offset the emissions from manufacturing. We believe the fair way of performing LCA is to include the impact at end-of-life (cradle to grave).Unless the material has an infinite lifetime, the carbon contained in the material will be converted back to CO2. With this approach, carbon negative seems unrealistic since the sustainable carbon sourcing CO2 benefit will be offset by the end-of-life emissions and the CO2 emissions during the manufacturing process. The best solution to minimize our impact remains a change of our consumption behavior: less meat, less plastics, less flights…
Yes, Bloom's ambitions are to become a technology provider through a licensing model.
Blooms focuses on lignocellulosic biomass, also called woody biomass which includes trees, straw, fruits stones and shells.
Solar, wind and hydropower enable the production of sustainable energy, but cannot provide the sustainable carbon needed to manufacture products of our daily life. CO2 capture from the atmosphere is very challenging due to the high dilution of CO2 (0.04 %). CO2 capture directly from relatively concentrated CO2 sources (eg. Outlet from a factory) is more feasible. Recycling is a great solution but cannot close the loop due to loss in collection and limited efficiency of recycling processes.
No, the Aldehyde Assisted Fractionation (AAF) is solely based on a chemical process. Bloom does not use biochemical methods.
The technology was born in the laboratory of sustainable and catalytic processing at EPFL with the idea of disrupting the way we look at plants: Instead of focusing on cellulose valorisation as historically performed by the pulping industry, the team’s approach was to center the process around lignin valorisation. Indeed, while lignin represents ca. 20% of the plants weight and is the fraction that most resembles petroleum – and hence has more chance to replace it – the industry has failed so far in extracting it. The technology is protected by several patents own by EPFL and exclusively licensed to Bloom, enabling us to increase valorisation from 40 to 80%.
All of our products are bio-based which means that their content originates from biomass/plants. The biodegradability of our products and their recyclability is a topic that we are investigating for each of them individually, as these are complex processes depending on a multitude of parameters, such as which product, what its use was, the environment it is supposed to degrade in etc. The clarification of those aspects is something Bloom is constantly working towards.
Let’s create a more sustainable future together.
Interested in learning more about how you can be part of the transition to a circular economy?